Large scale packaging design
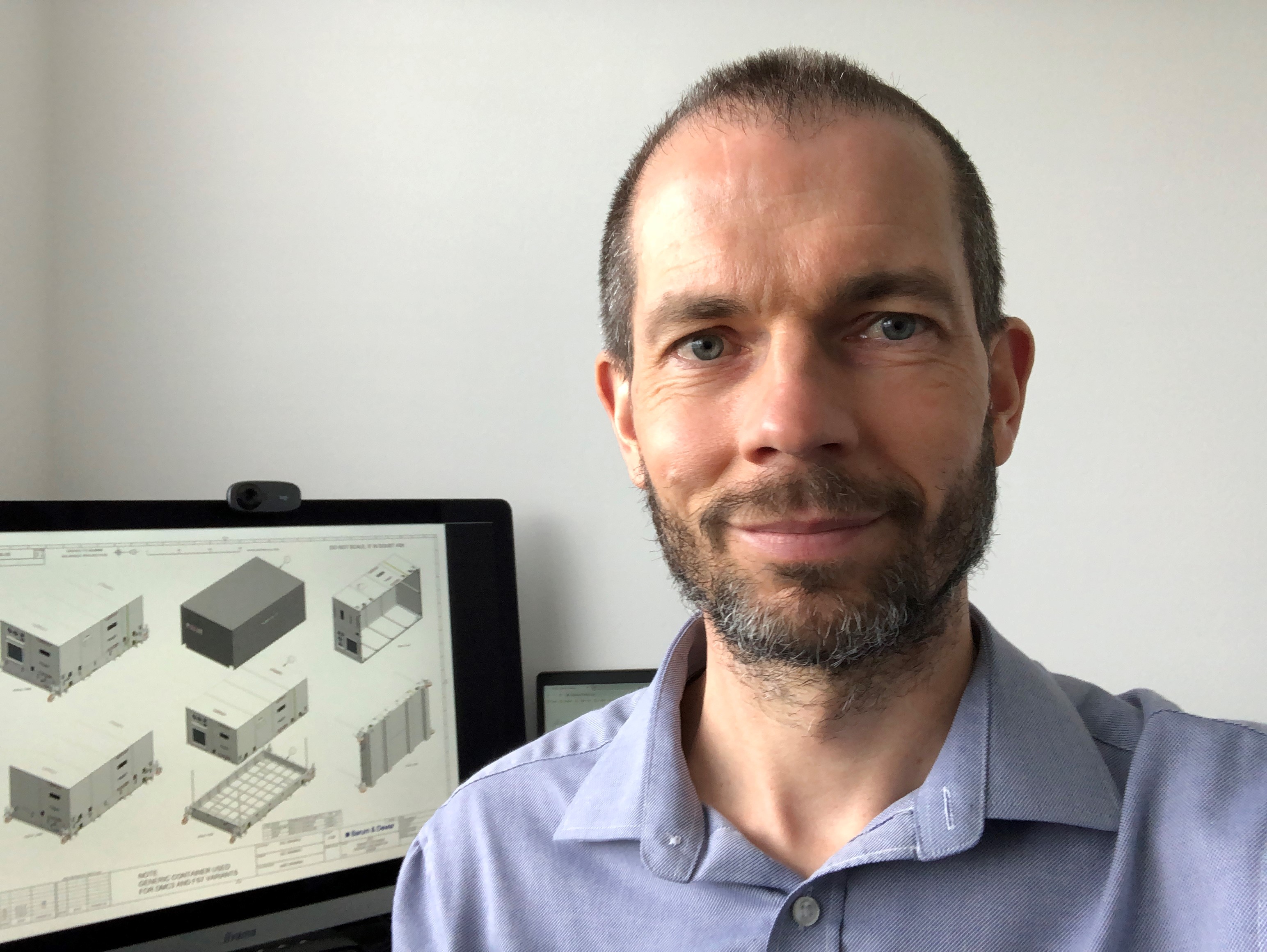
Dave Rouse, our Technical Design Engineer, discusses all things large scale packaging design, from initial client briefs to technical challenges and the finished product.
Barum & Dewar has a long history of supplying large, bespoke containers to key clients in the space and defence sector and work alongside businesses such as Airbus, SSTL and the Ministry of Defence. In the space sector, our large bespoke containers are used to transport equipment such as satellite hardware including small satellites, parts for larger satellites and a number of related items. In the defence sector, we’ve developed bespoke packaging for a wide array of equipment with some of the largest containers being for submarine periscopes.
We work closely with our clients on these types of projects to ensure we design a product that is completely fit for purpose and will match their needs. At the initial stage we run through how they intend to use the product through its whole lifecycle so we can establish what features they need, for example if it needs waterproofing or must be airtight or whether it will need lifting points or forklift points. We’re not afraid to question and challenge our clients to make sure we design something that works completely for them, and we’ll never take the easiest option.
When designing products to such a large scale there are many factors to be taken into consideration. One of the biggest challenges we face is designing something that’s as compact and lightweight as possible whilst still being completely robust so it’s important for us to get this right. Our Creo 3D CAD modelling system helps us visualise the entire product at the design stage so we can test different scenarios and ultimately find the right balance.
There are also several technical challenges throughout the design process, one of these being selecting the appropriate shock mounts so that when the equipment is subject to vibrations and movement during transit it isn’t at any risk of being damaged. To mitigate this, we work closely with shock and vibration control specialists, Socitec who run advanced calculations with our client’s data, for example the item’s maximum G loading, to determine the correct shock mounts.
Something we are seeing more often with our large bespoke containers, especially concerning space hardware, are more stringent health and safety procedures coming into play which is leading to higher test ratings. For example, on large containers the testing ratings we used to see were around 1.2x the gross mass but now some clients are requesting 2.5x so we’ve had to change the way we design. We’re very adaptable to our client requirements so we’ve been able to accommodate this well.
We see our clients coming back to us time and time again for large, bespoke packaging and that is down to the interaction and collaboration we have with them throughout the entirety of the project. Our clients feel assured we will deliver a product that works for them because we are focused on asking the right questions and are obsessive about detail. This translates directly into the quality of our products as we are so committed to getting the design right from the very beginning.